BTEX is a well-known and heavily-regulated group of volatile organic compounds emitted from a wide variety of industrial facilities. Eliminating BTEX requires some basic knowledge about each of the compounds work.
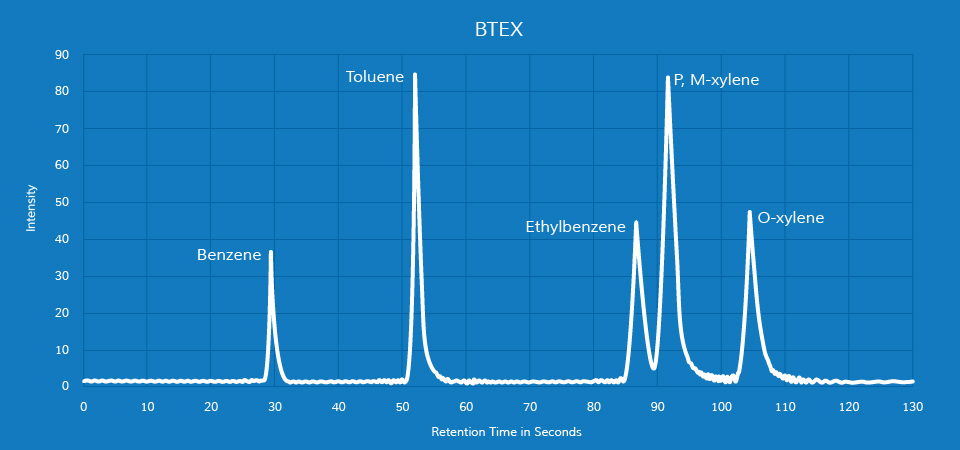
BTEX is a well-known and heavily-regulated group of volatile organic compounds (VOCs) emitted from a wide variety of industrial facilities. Each of the compounds is harmful to humans, so they’re regulated to varying degrees around the world by public health and worker safety organizations.
BTEX emissions can be detected and eliminated. Understanding how this is done requires some basic knowledge about each of the compounds, including:
- Where they naturally occur.
- How they’re used in industrial applications.
- How they impact human health.
- How they’re identified and regulated.
- How they can be eliminated.
BTEX background
BTEX is an acronym for four common VOCs found in industrial settings: benzene, toluene, ethylbenzene and xylene. They’re well-known hazardous compounds found in a wide variety of facilities and products, but they all naturally occur in crude oil and natural gas. Their escape into the environment is most often a result of the refining processes of each; they’re also used in various industrial and pharmaceutical processes.
Benzene – C6H6 – This colorless, sweet-smelling compound evaporates quickly and is highly flammable. It naturally occurs as a component of crude oil and natural gas and can also be found in the smoke from volcanoes, forest fires and cigarettes. The compound can be captured during the crude oil refining process and was once a prominent gasoline additive as a substitute for lead.
Benzene is extremely harmful to humans. Low levels of exposure can cause drowsiness, dizziness, confusion, rapid or irregular heartbeat and tremors. Long-term exposure to benzene is known to cause cancer; extremely high concentrations of benzene are fatal. The U.S. Environmental Protection Agency (EPA) mandates that gasoline can contain no more than 0.62% benzene by volume. The U.S. Occupational Safety and Health Administration (OSHA) mandates a benzene Permissible Exposure Limit (PEL) of 1 ppmv over an eight-hour workday or a peak limit of 5 ppmv over 15 minutes.
Toluene – C7H6 – Toluene is a colorless liquid with a strong solvent smell. It’s a minor constituent of crude oil captured during the refining process and used in the production of glues, resins, solvents, paint thinners, lacquers, fingernail polishes, adhesives and plastic products.
People exposed to toluene experience effects similar to drunkenness. Long-term exposure can lead to vision and hearing loss. It is not a recognized carcinogen. OSHA’s PEL for toluene is 200 ppmv over an eight-hour day.
Ethylbenzene – C6H5CH2CH3 – This colorless, sweet-smelling compound is gaseous at room temperature and is highly flammable. Derived from crude oil during refining, ethylbenzene is widely used in the manufacture of styrene. It’s also commonly used as a solvent in inks and dyes and is a byproduct of the burning of motor fuel.
Exposure to high levels of ethylbenzene can cause hearing loss and kidney damage; it can also lead to the formation of cancerous tumors. The EPA mandates that drinking water can contain no more than 700 ppbv of ethylbenzene; OSHA’s PEL for the compound is 100 ppmv over an eight-hour day.
Xylene – C6H4(CH3)2 – The compound comes in three isomers (identical chemical formulas in different structures). It’s a colorless, greasy flammable substance used in the manufacture of plastics and polyester clothing. It’s also widely used as a solvent.
High levels of xylene exposure can cause headaches, poor coordination, dizziness and confusion. At high levels over short periods of time, exposure can also cause skin irritation. It’s fatal at extremely high levels, but it is not recognized as a carcinogen. The EPA mandates that drinking water contain no more than 10 ppmv of xylene; OSHA’s PEL for the compound is 100 ppmv over an eight-hour day.
Note, however, that OSHA has acknowledged its PELs for hazardous compounds are outdated—some of them haven’t been updated since the Administration was created in 1970. Other organizations have developed their own stricter PELs, which OSHA has published here.
Identifying BTEX compounds
BTEX emissions can either be passively or actively measured:
- Passive measurement – Badges or tubes that absorb or collect BTEX compounds at known rates are set at monitoring sites and then collected later. The samples are then sent to labs where BTEX concentrations are identified using ion chromatography or plasma mass spectrometry.
- Active measurement – Gas chromatograph mass spectrometers are installed at facilities to collect air samples. These systems can identify total VOC emission concentrations as well as concentrations of individual compounds in a matter of minutes. However, these systems are much more sophisticated and therefore much more expensive.
Placement of measurement equipment outside a facility is critical. Unpredictable ambient conditions mean readings become less accurate the farther away from an emission site the equipment is placed.
Treating BTEX emissions
Because BTEX is so strictly regulated in the U.S. and around the world, there are many ways to remove it, including:
- Isolating the compounds during refinement or manufacturing processes and preparing them for reuse or sale elsewhere.
- Utilizing available treatment technology, including biological degradation or adsorptive filtration.
- Diverting the compounds from processing or manufacturing and burning them off.
Some removal methods solve the problem more completely than others. For instance, reusing or selling BTEX compounds merely delays their eventual emission. Activated carbon filters are expensive and must be frequently replaced as their performance wanes over time. Burning BTEX compounds is almost as bad as just letting them escape untouched because one of the byproducts of their combustion is CO2.
Other natural means of eliminating BTEX compounds exist. For instance, some of the compounds degrade in natural sunlight. Accordingly, combined ozone (O3) / UV radiation systems can eliminate the compounds. However, these systems require constant replenishment of ozone, which is very unstable. Also, UV treatment requires lots of energy, so these systems are quite costly over time.
The compounds can also be metabolized by microorganisms under both aerobic and anaerobic conditions. This resource provides a more detailed explanation of these metabolic degradative pathways.
Innovative biological BTEX treatment
BioAir Solutions designs and builds aerobic biological treatment systems that naturally degrade the harmful BTEX compounds, without the downsides inherent to other treatment methods.
These systems, such as BioAir’s EcoFilter® biotrickling filter, take up significantly less space than any other treatment solution, do not require constant replacement of filtration media and are very inexpensive and easy to maintain. In addition, performance testing of BioAir systems show they routinely outperform competing industrial emission mitigation methods.
Through our BioAir Complete® process, our scientists and process engineers take a consultative approach to industrial emission control. If you want to discuss a BTEX emission challenge at your facility, request a consultation. If you’re still researching, try reading our guide to industrial odor and emissions control.