


Start-to-finish odor control engineering for polymer manufacturer
BioAir system helps get to the root of the problem and put Purolite’s facility on a path to a reliable solution
HIGHLIGHTS
• Odor problems bothering neighbors and flagging regulators
• Expert site visit diagnoses odor sources and poor performance of current equipment
• Upgraded chemical scrubber installed, along with system designed to support it for years
Unpleasant odors can bring unwanted attention to your industrial facility. This was the case at the Philadelphia location of Purolite, a manufacturer of ion exchange resins that separate, remove and recover very specific elements and compounds.
The persistent smell didn’t prevent them manufacturing high-performance resins. But complaints from neighbors and visits from regulators can easily turn into a risk to productivity — and reputation.
In this case study, we’ll outline how Purolite enlisted BioAir to get to the root of the problem and put their facility on a path to a reliable solution.
PROBLEM
Odor complaints and a choice to make
The two departments of the Purolite facility consist of cation production and anion production. These small-but-mighty powders are used in a range of applications, from water softeners to drugs that help surgeons identify certain types of cells in tissues.
In the anion production line, the wastewater released a fishy, urine smell that caught the attention of neighbors who alerted the Philadelphia Department of Public Health.
The regulators misunderstood the issue and tested for VOC emissions, which Purolite passed with no issue. Months later, after another series of odor complaints, regulators returned with the same result.
“We didn’t want to just hold up our permit to operate and say we’ve done everything we need to.”
Les Confer, Senior Process Engineer at Purolite
The Purolite team was at an impasse. They were pleased to not receive any penalties from the Department of Public Health, but city regulators provided no clear direction on remedies (the odor issue being beyond their area of expertise). And it wasn’t as if there were zero odor control solutions in place; an existing chemical scrubber on the property seemed to be operating normally.
“Even though we weren’t getting in formal trouble, we wanted to avoid this loop of city visitors,” said Les Confer, Senior Process Engineer at Purolite. “We didn’t want to just hold up our permit to operate and say we’ve done everything we need to.”
So Les and his team looked at their options — which led them to BioAir’s odor assessment process.
“I felt as I researched what was out there, there was nobody else doing that,” said Les. “We didn’t want to try to be smarter about what we’re doing than people in the scrubber business.”
SOLUTION
A revealing site survey and odor study
Accurately understanding the cause of odor problems is crucial to success — otherwise, you run the risk of solving the symptoms instead of getting to the root of the problem.
The BioAir process begins with experienced BioAir scientists conducting an evaluation on your site. These experts are well-versed in the science of odors and emissions as well as the industrial processes that cause them.
Matt Johnson, Industrial Sales Manager at BioAir, kicked off Purolite’s assessment with a site survey on the anion production line. He saw that all the drains from the anion processes drained to a sump tank. The turbulent water streams were open, uncovered and warm — all contributing to the odor problem.
“I saw this and immediately knew we needed to cover and vent the sump tank,” said Matt.
Matt also found that the existing chemical scrubber was not properly sized for the application — for instance, the ductwork leading to the system was improperly sized, creating pressure and airflow problems for the system.
An odor study allowed Matt to paint the full picture for Les and his team. The odor study confirmed VOCs were not the problem. Rather, the level of amines and ammonia were the drivers. In fact these were some of the highest compound concentrations ever encountered by BioAir: 2,177 ppm of amines and 438 ppm of ammonia.
This information gathered in the odor study arms your odor control partner with the necessary data to solve the problem head on.
“I think the odor study for the amine generating department led us to intelligently make a $250,000 capital equipment purchase for the entire BioAir scrubber,” said Les. “You’re penny wise and pound foolish not to get that odor study to know that you’re proceeding with good design and criteria.”
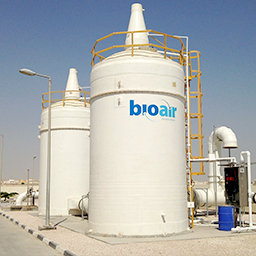
Systems built to solve your problems
See the odor and emission control systems we customize to your site and its unique challenges.
RESULT
Value-added engineering from a trusted partner
Armed with the information from the site survey and odor study, Matt returned to the Purolite team with equipment and system design recommendations.
Selection of the correct treatment equipment requires expert knowledge. Professionals like Matt know the difference between what makes sense on paper — and what will actually function in your facility environment.
Based on the sources of the odor, two options were viable: a chemical scrubber or an adsorptive carbon filtration system. But because of the high concentrations of odor-causing substances, carbon filtration would be prohibitively expensive due to the constant need to replace the media.
“If we did adsorption, it would have killed the carbon in a month,” said Matt.
As the facility already had a chemical scrubber, our Qimi® chemical scrubber fit right in with their production processes.
Selecting the right scrubber is only part of the solution. Matt also provided Les with a full system piping design, including specific instructions for the ancillary equipment, ducting and controls. Details like correctly sized ducting, manifolds and control valves ensure the equipment will efficiently neutralize the odor-causing amines and ammonia.
And most importantly, this extra guidance gave Les the confidence he chose the right partner.
“I feel that with another scrubber competitor I might have chosen that they would’ve really left me alone to hang myself,” said Les. “I would not have wanted to do this project without a company like BioAir that stayed with us.”
Need to replace dysfunctional odor control equipment?
Odor control projects tend to invite challenging design and delivery conditions. Enlisting a vendor with imperfect engineering or unresponsive communication puts on-time delivery and project success at risk.
If you’re looking for an air treatment partner with demonstrable expertise and performance-guaranteed equipment, reach out. We’d love to talk about current or future projects.

Find your local BioAir sales representative
