


Eliminating waste-to-energy odor with teamwork and strong engineering
For five years and counting, Yarra Valley Water’s food waste-to-energy plant has powered itself and its neighboring Aurora sewage treatment facility.
HIGHLIGHTS
• Australian wastewater treatment facility identified a waste-to-energy opportunity
• Two EcoPure® reactors remove 99.5+% of inlet hydrogen sulfide (H2S)
• No fugitive odors have been released from the system since installation
Waste-to-energy facilities divert large volumes of waste from landfills and use that waste to produce clean energy. Their performance of this dual function provides enormous value to companies and communities.
In 2017, Yarra Valley Water in Victoria, Australia, identified a waste-to-energy opportunity. Their Aurora wastewater treatment facility, on the edge of the Melbourne metropolitan area, generated a large volume of dry solids by filtering wastewater. Like most wastewater treatment facilities, they also consumed a huge amount of electricity.
If they could supplement their dry solids with organic waste, like compost or restaurant grease, from elsewhere in the community, then they could fuel a waste-to-energy facility with the biogas from that organic material and mitigate their own energy costs.
But there’s a reason dedicated waste-to-energy facilities aren’t in every city. They present a number of challenges.
For starters, because the technology used to generate energy from waste is often unfamiliar to technicians, it can prove costly to implement and challenging to operate. Availability of the waste source material can vary significantly making steady-state continuous operation unpredictable. Variations in the quality of the available waste is another issue requiring management.
So when Yarra Valley Water envisioned a greenfield food waste-to-energy project next door to their wastewater treatment plant, they hired Aquatec Maxcon to design and install the project — a company who defines success as ideal performance with minimal operator inputs and service.
PROBLEM
The greenfield odor challenge for Yarra Valley Water
Waste-to-energy plants reek. The waste and various processes throughout the plant release enough odor to necessitate specialized air treatment systems. By the time they were approached about this project, Aquatec Maxcon already had the odor control partner they knew they could rely on— BioAir Solutions.
Trustworthy odor control is necessary to any viable waste treatment facility. “A main aspect of any waste site is that no one knows it’s there,” said Denham Melder, Aquatec’s odor control specialist. “That means there can’t be any odor emitting from a facility.”
Usually, the first step in developing odor control systems is to diagnose the odor on site or through sample testing. But that was impossible for Aquatec and BioAir due to one simple fact: the facility didn’t exist.
“A main aspect of any waste site is that no one knows it’s there.”
Denham Melder, Aquatec odor control specialist
Engineering an odor control system is complicated enough when responding to measurable or predictable inputs, but Yarra Valley Water had no way of knowing the type or volume of food waste that would be dropped in their bays. Engineering a feasible system would involve knowledgeable forecasting, calculated risks and serious expertise.
SOLUTION
An engineering process focused on feasibility, economy and trustworthy performance
The system BioAir proposed based on initial estimates of inlet compound concentrations was too expensive to implement, so we worked together with Aquatec to carefully reassess some of their estimates. We pointed out concentrations that looked high and suggested areas to dial back the scale of our system — reducing cost while still confidently meeting performance goals.
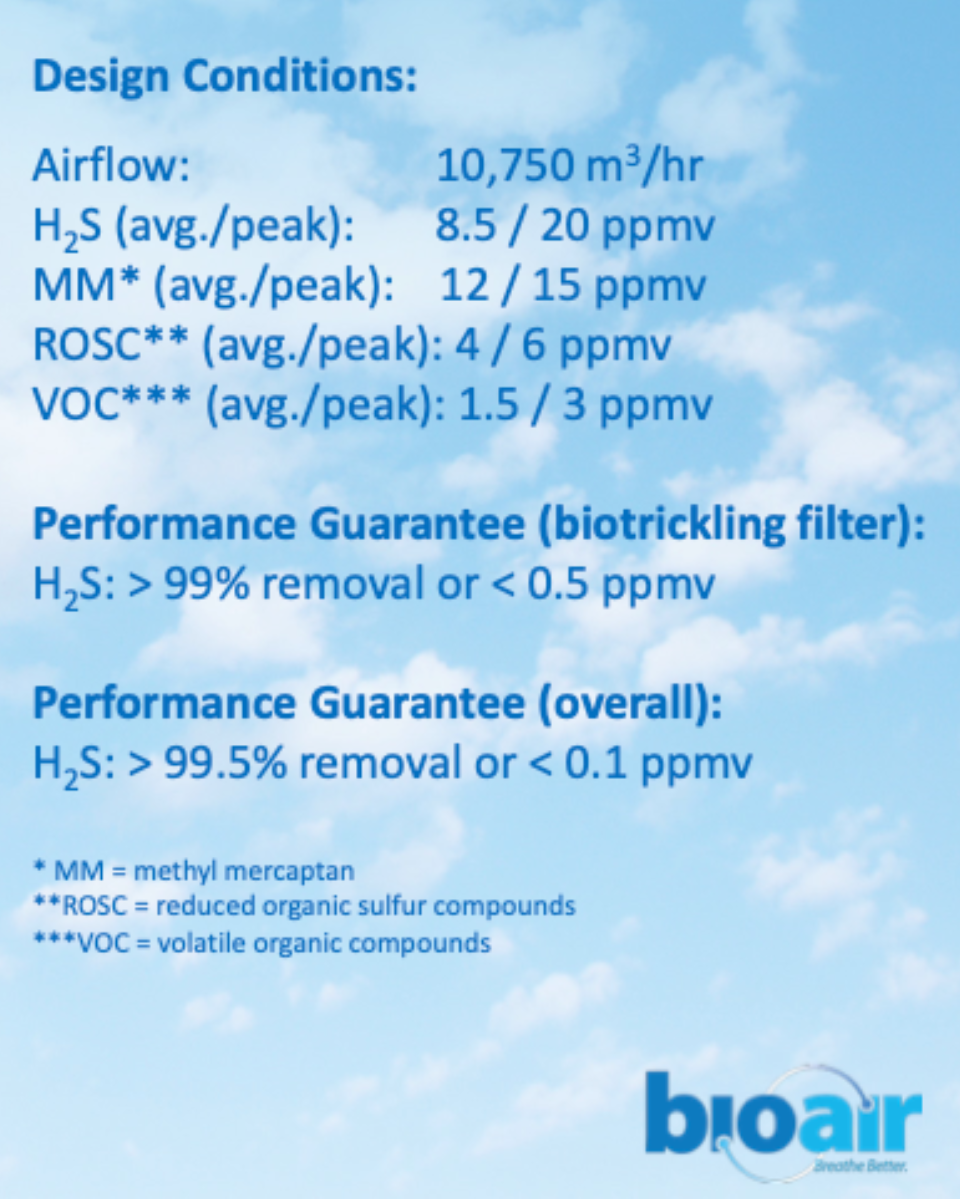
In the end, BioAir engineered a system built around two EcoPure® reactors, which combine biological treatment and carbon filtration technologies in a single reactor to deliver remarkably clean outlet air. Foul air first passes through the biotrickling filter, which removes almost all of the offending compounds. Next, the carbon filtration section takes care of the rest.
The key advantage of our dual tech system is that air entering the second stage of treatment is already very clean. This results in much longer life of the carbon media, which is expensive to replace. Therefore, the dual tech system would cost much less to operate and maintain than standard adsorption technology.
“Aquatec Maxcon had a really strong process engineer who had reached out to me ahead of the project to talk about odor control at the plant,” said Matt Johnson, Industrial Sales Manager at BioAir. “He and I talked through our equipment, and we also helped them design the odor collection duct work. It was really a BioAir Complete® process without the site sampling — because this installation did not yet exist, there was nothing to sample.”
This relationship is crucial on complex projects. An odor control system designed without expert process planning would be doomed to failure, and Aquatec was busy designing the full waste-to-energy plant. Diligent engineering and adept integration of equipment from a range of suppliers drove BioAir and Aquatec Maxcon’s success on the project.
Communication between parties about full system design allowed both teams to diagnose this challenge and overcome it quickly. Denham appreciated BioAir’s transparency and willingness to help with the overall facility design. “They supplied a large amount of information that allowed our design team to know exactly what was required.”
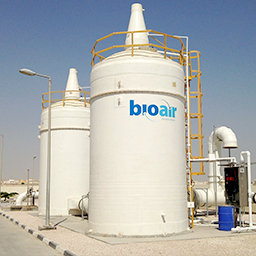
Systems built to solve your problems
See the odor and emission control systems we customize to your site and its unique challenges.
RESULT
Complex system performance delivered simply
Throughout numerous system design iterations, the odor control project’s goal never changed: The Yarra Valley Water waste-to-energy plant needed complete odor removal. Our EcoPure® system proposed to achieve this via removal of 99.5+% of inlet hydrogen sulfide (H2S) and additional removal of other odorous compounds like mercaptans and reduced organic sulfur compounds.
As water treatment industry leaders, Aquatec knew that the best treatment systems meet performance needs for years with minimal fuss. Since the plant’s staff didn’t specialize in odor control, the BioAir system needed to operate simply without frequent service. And it needed to do so for a long time.
The value of BioAir’s assistance with the overall facility design was borne out initially by the project finishing on schedule. The quality of BioAir’s duct engineering and teamwork with Aquatec revealed itself once the plant started accepting large amounts of unpredictable bio waste.
Five years later, we can call the project an unmitigated success. According to Denham, “No fugitive odors have been released from the system since installation. And since commissioning there has been no need for support from BioAir — the system operates as required with minimum input.”
For five years and counting, Yarra Valley Water’s food waste-to-energy plant has powered itself and its neighboring Aurora sewage treatment facility. Most waste-to-energy projects can’t fully power wastewater treatment facilities, but Yarra Valley Water actually exports excess electricity back onto the power grid. You can read about the facility’s impact here.
Need odor control on a complex project?
Waste-to-energy facilities are great examples of complex projects that tend to invite challenging design and delivery conditions. Enlisting a vendor with imperfect engineering or unresponsive communication habits invites problems that ripple through the project and put on-time delivery and project success at risk.
If you’re looking for an air treatment partner with demonstrable expertise and performance-guaranteed equipment, reach out. We’d love to talk about current or future projects.

Find your local BioAir sales representative
